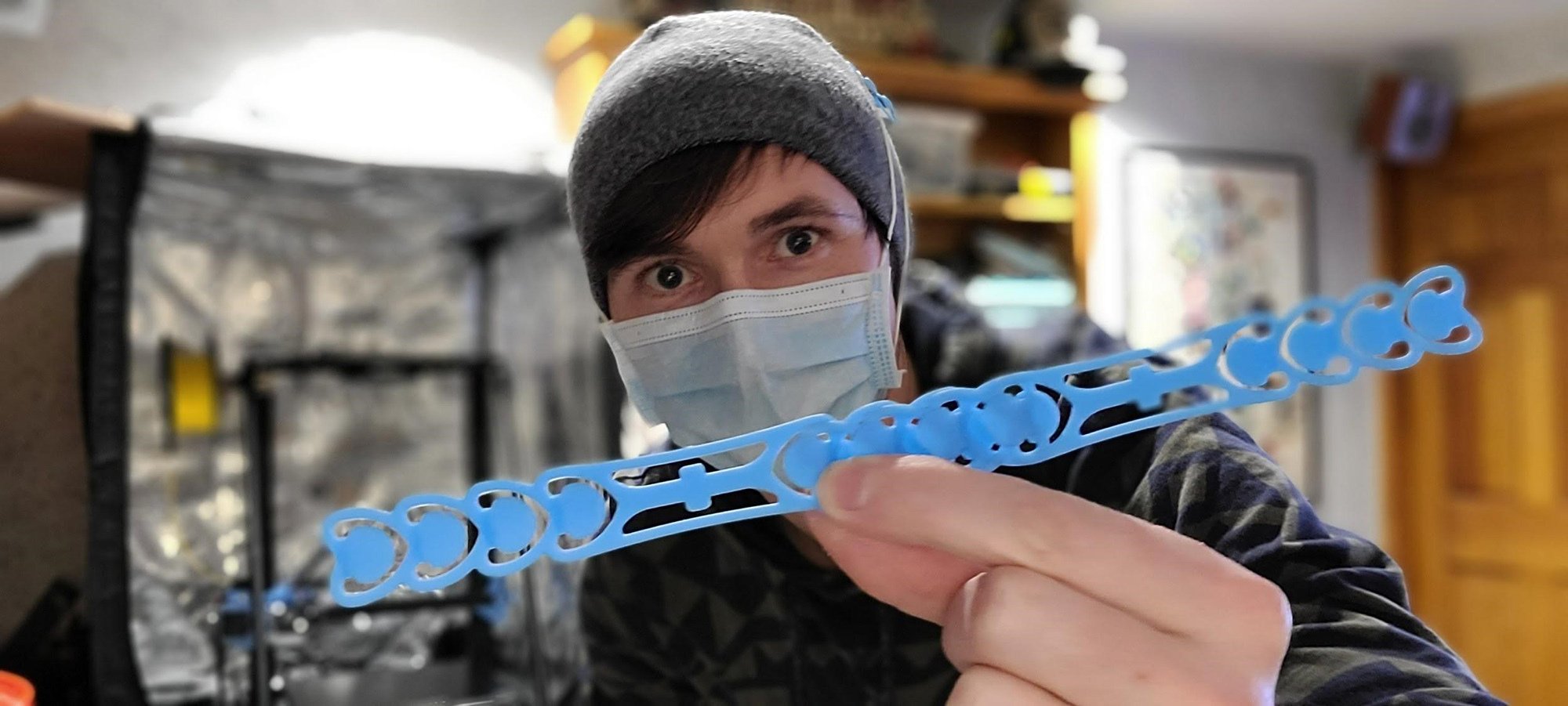
EarLove Mask Adjusters
From Open-Source Community Project to Scaled Industrial Solution
EarLove is a human-centered mask adjuster I designed to solve the global problem of ear pain from prolonged mask-wearing during the COVID-19 pandemic. The project began as a freely available, open-source design for the 3D printing community and evolved into an injection-molded product that was deployed by the thousands to frontline workers. It's a story of rapid, user-focused innovation, from a personal maker project to a scaled industrial solution.
Amazon Article: How a small piece of plastic helps keep employees safe
Thingiverse.com: The "SeaMass" Modular Ear Saver Design - Thin, Flexible, Versatile
Amazon.com: Ear Love Mask Adjuster
Open Source & Community Iteration
As the pandemic began in 2020, the open-source 3D printing community really stepped up to help frontline workers by printing and donating PPE in massive quantities. At the time I owned four 3D printers and wanted to help out!
I decided to start printing “Ear Savers”, a very popular model that was being printed all over the globe and donated to hospitals. Upon reviewing the comments on the design, and printing a few myself, I quickly realized the need for a more efficient and effective "ear saver" design.
If I could design a better solution that required a fraction of the time and material, it would have a massive impact on the global scale. So I developed and published my design—initially called the "SeaMass" modular ear saver—on Thingiverse in April 2020. I shared it freely, optimizing the design for home 3D printers and encouraging community feedback.
The core innovations shared with the community were:
A Modular, Linkable System: A unique internal tab design allowed units to be use individually or linked together for a custom fit on any head size or for different wearing styles (behind the neck or over the head).
User-Centric Design: Unlike other designs with external prongs that tangled in hair, mine featured a smooth outer perimeter with internal tabs to prevent snagging.
Material Efficiency: The design was engineered for fast 3D printing with minimal material use, allowing makers anywhere to produce them quickly and cheaply.
This open-source phase was crucial for validating the design's effectiveness and gathering real-world feedback.
Scaling for Impact & Industrial Production
The design's success within the maker community demonstrated its potential for broader impact. To meet the urgent demand from frontline workers, the project needed to scale beyond the capacity of 3D printing.
This led to the next phase:
Design for Manufacturing (DFM): I re-engineered the validated design for mass production via injection molding, adapting the geometry for tooling while preserving the core features that made it successful. The material was switched to durable and recyclable polypropylene.
Corporate Adoption & Distribution: The project gained internal support at Amazon, which recognized its value for employee safety and comfort. Now named EarLove, the adjuster was produced and shipped to over 130 Amazon and affiliate facilities.
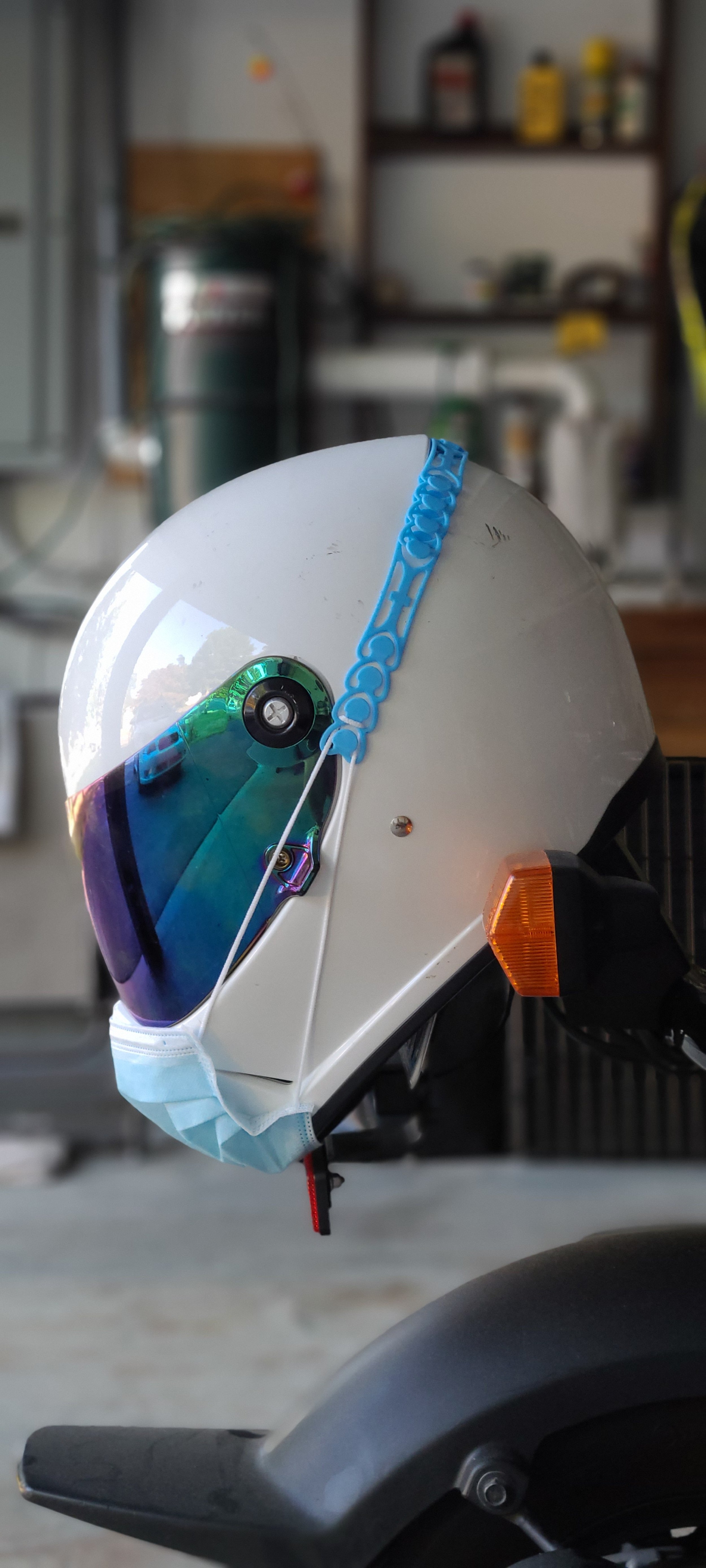
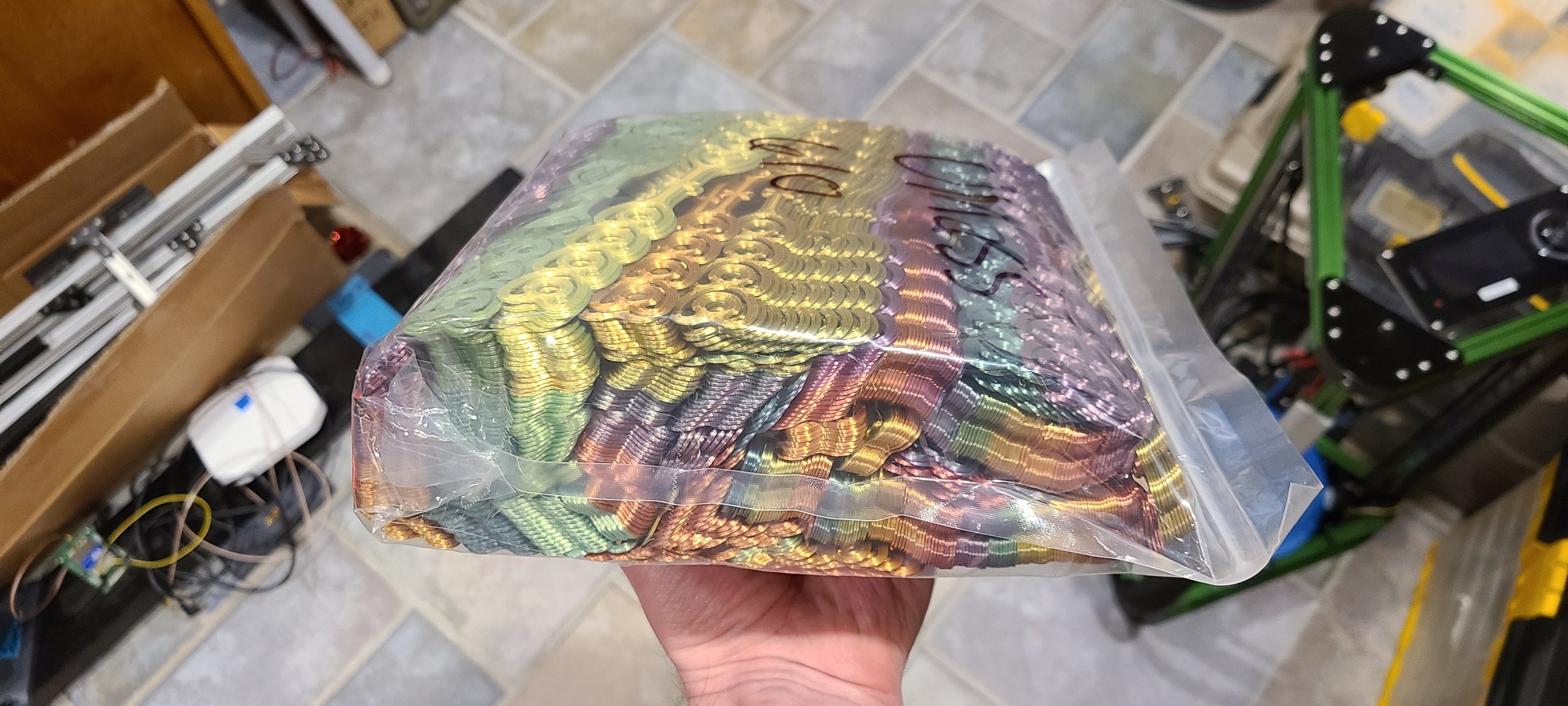
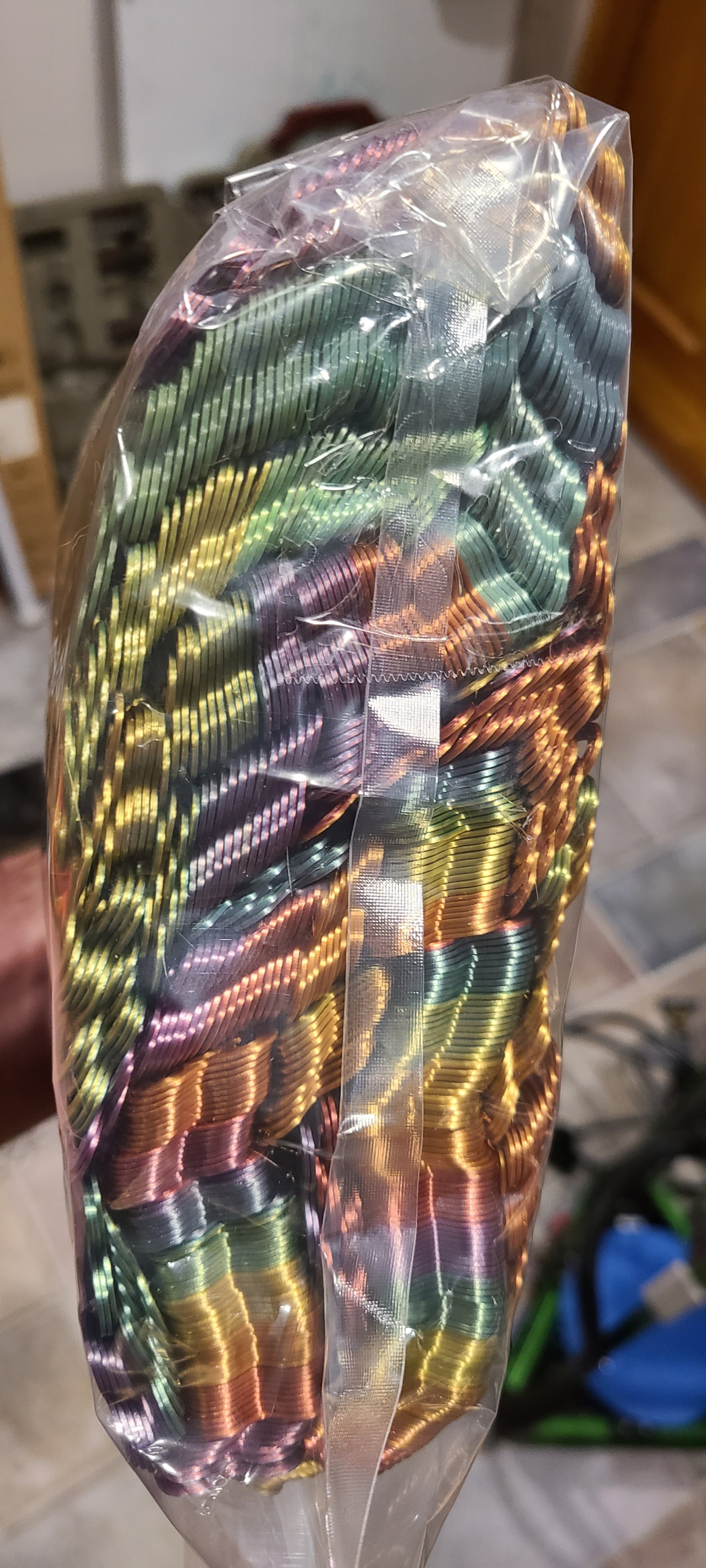
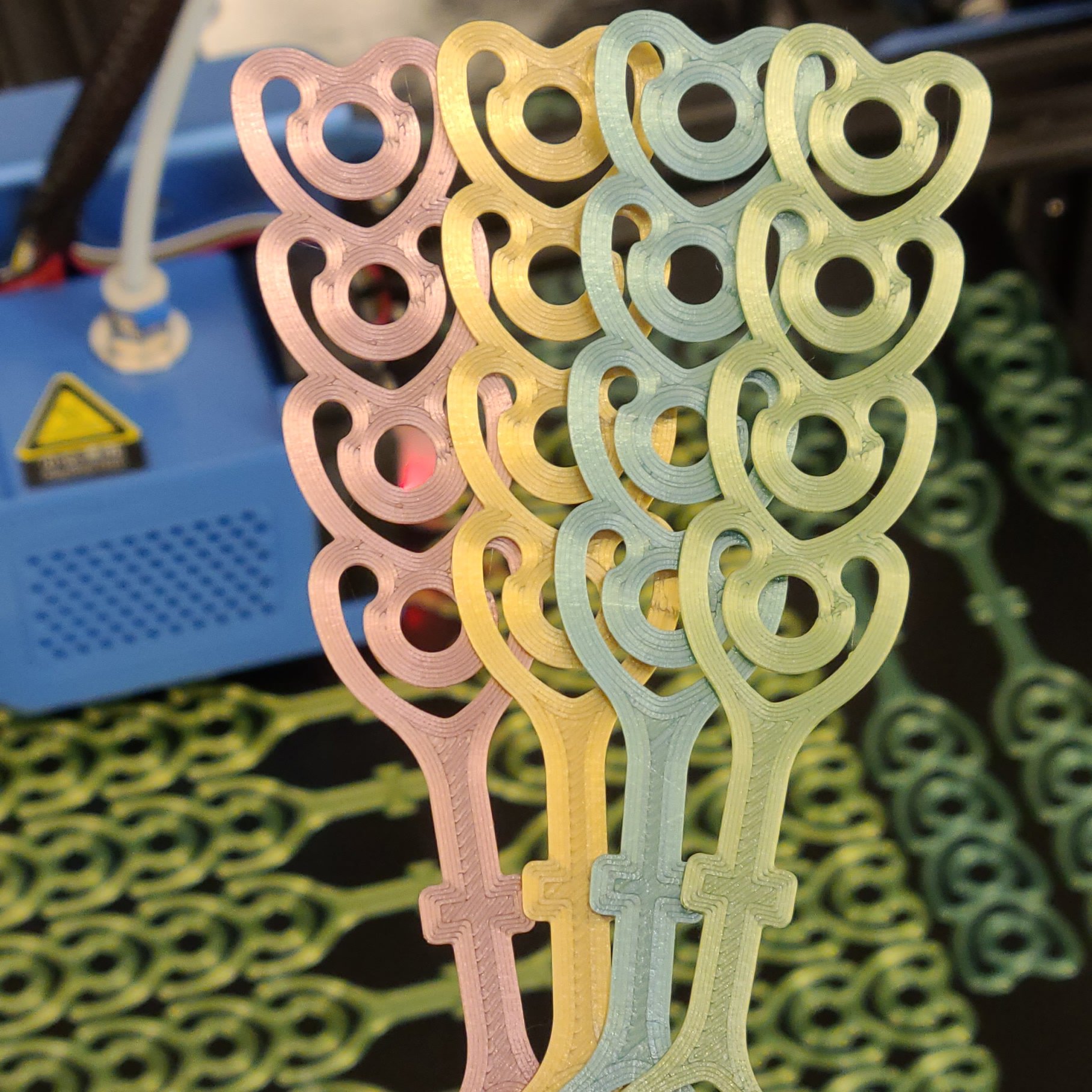
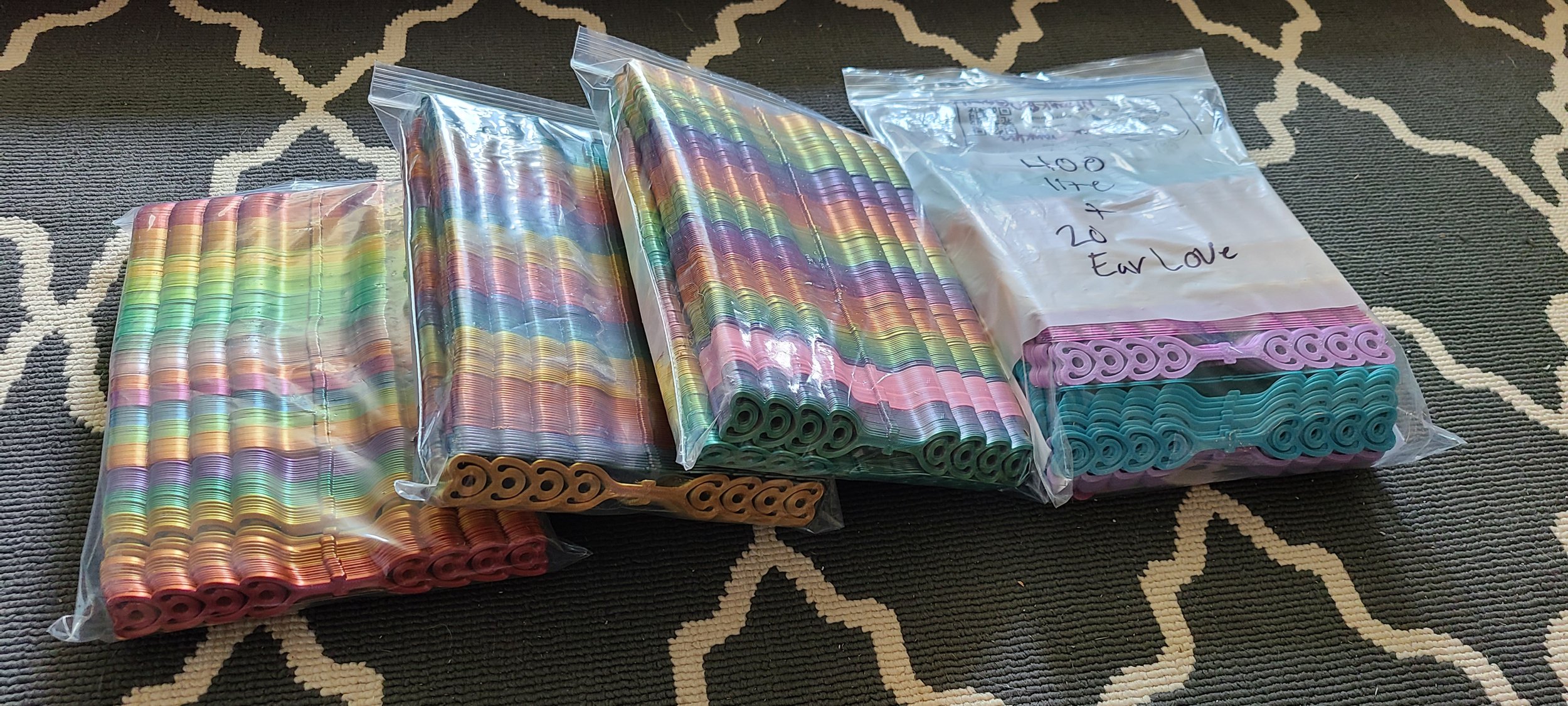
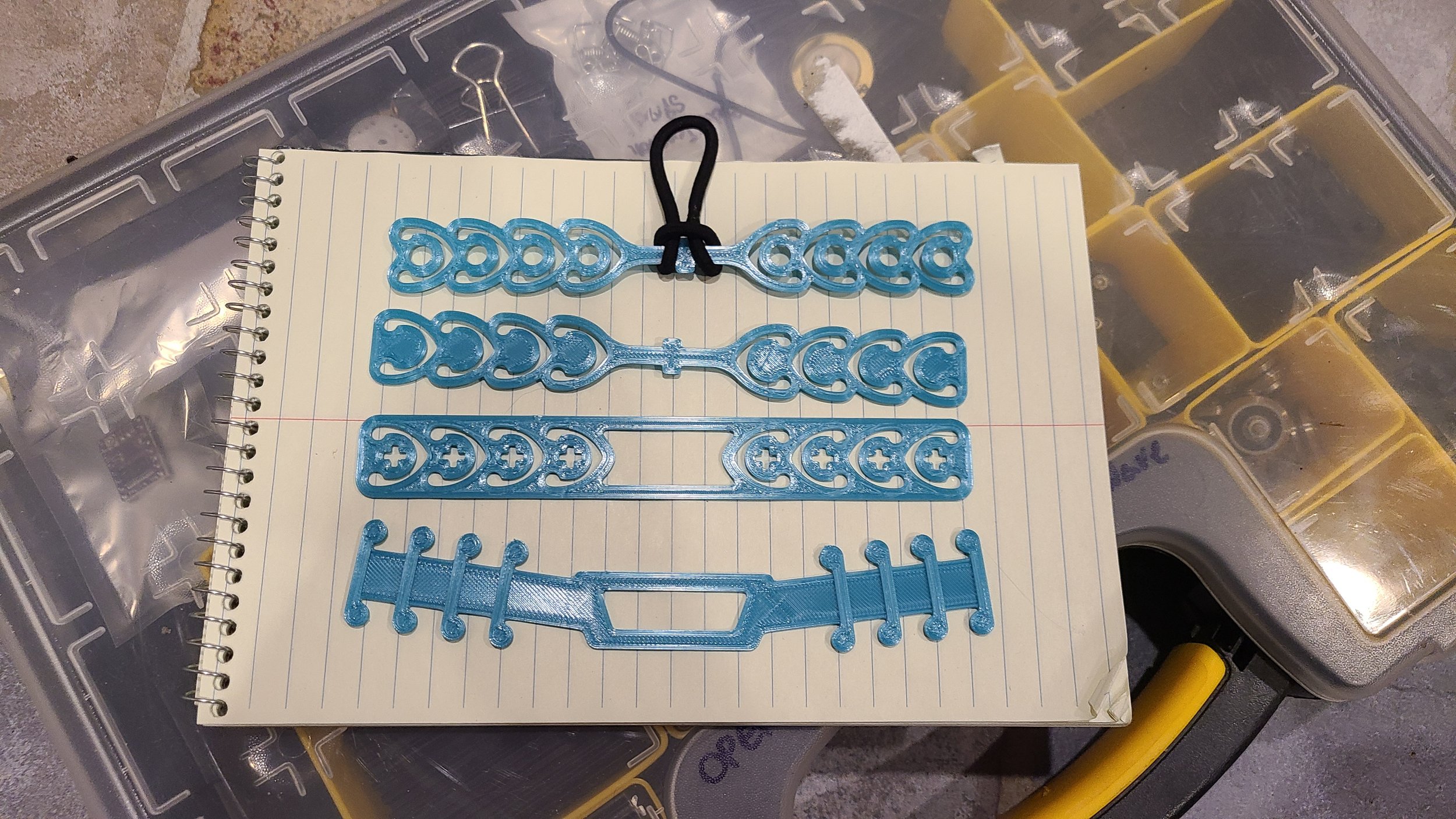
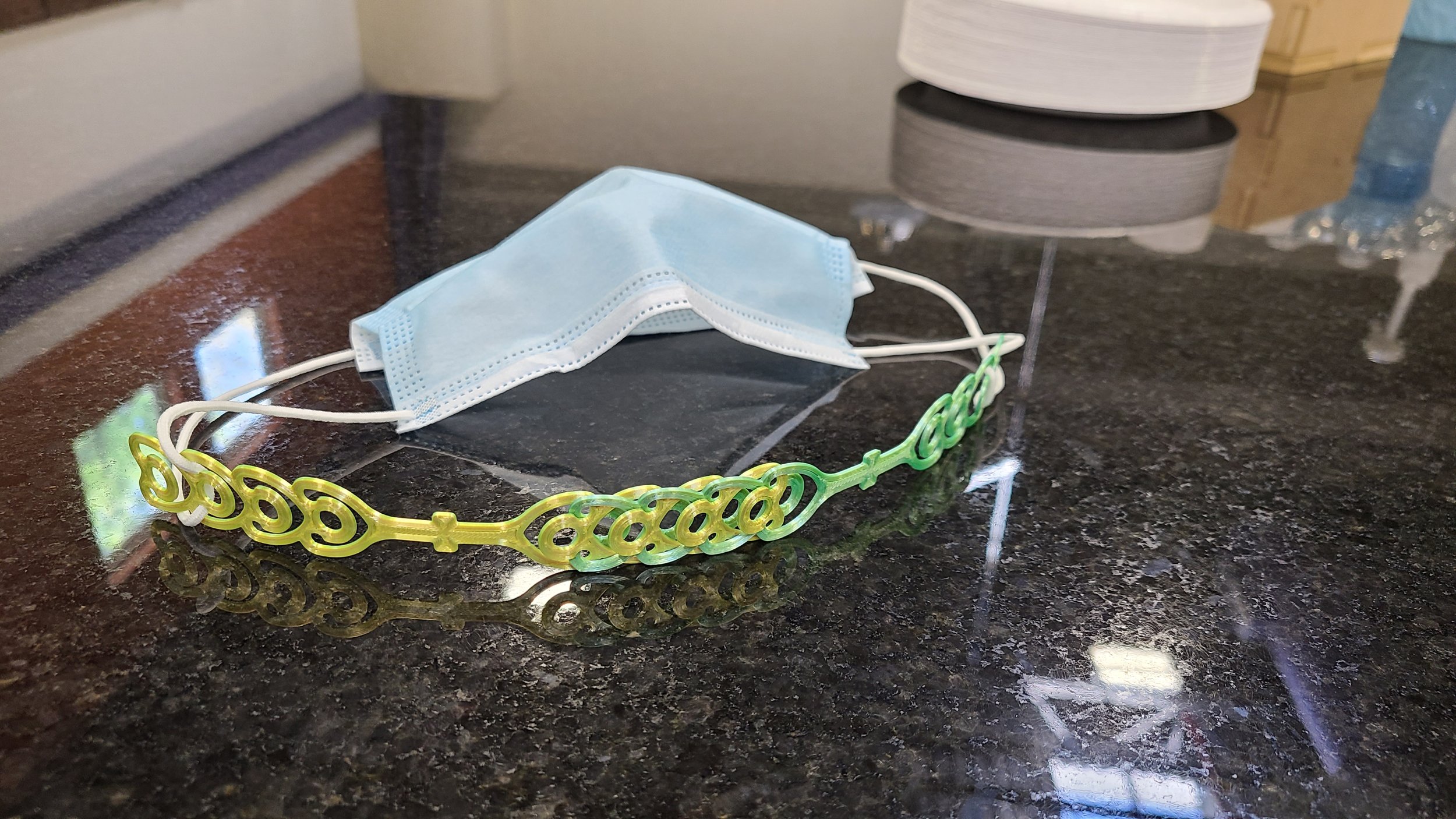
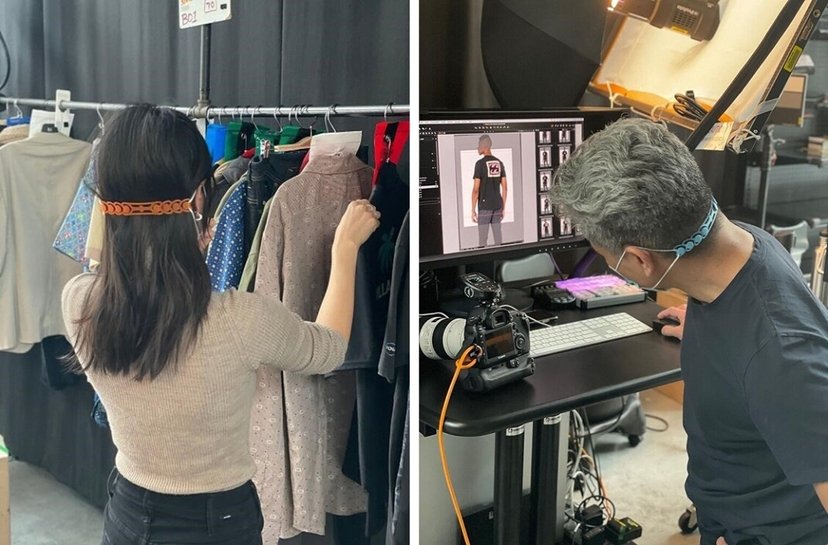
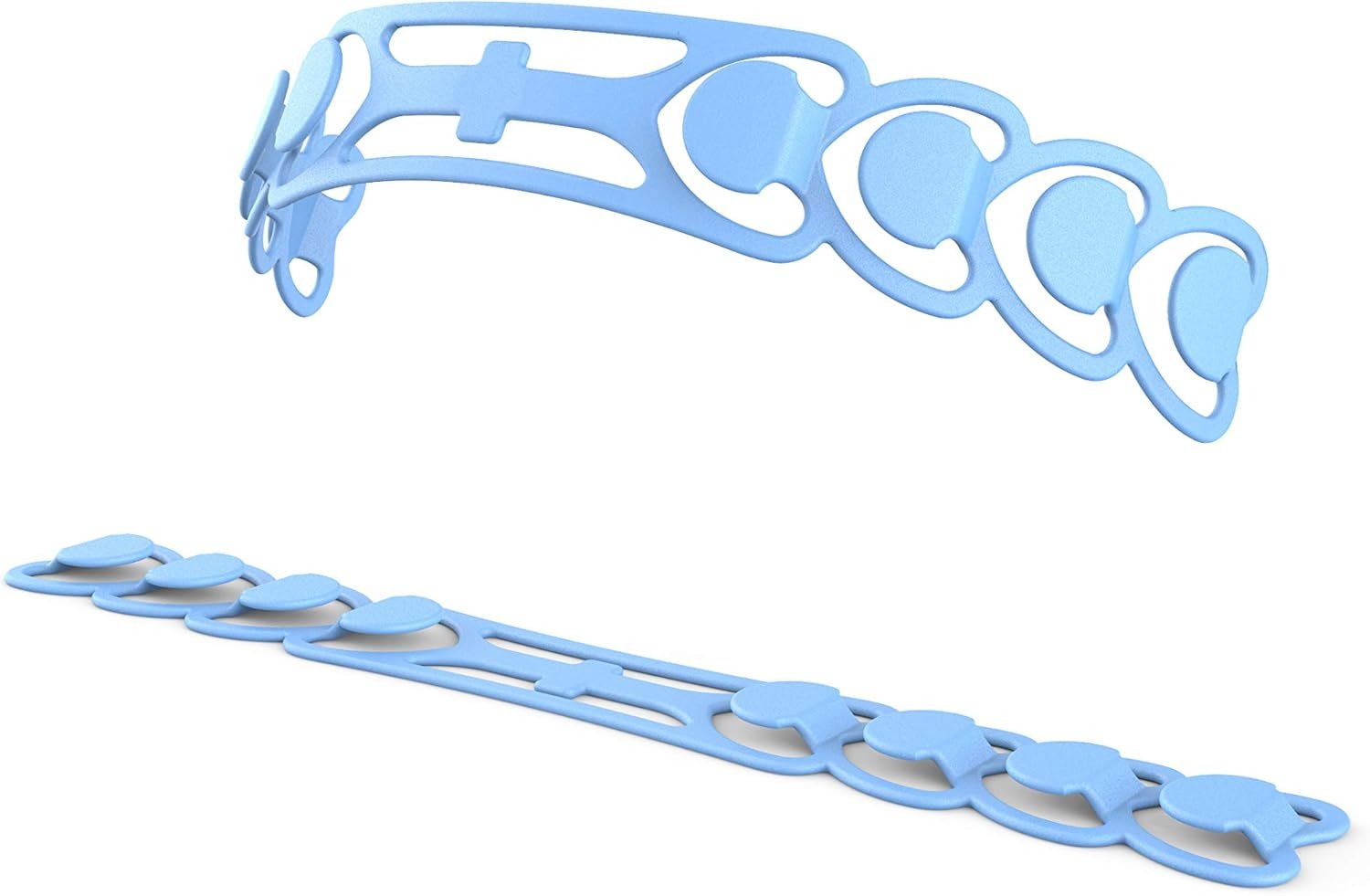
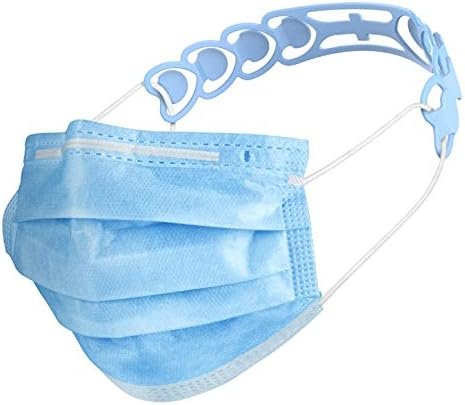
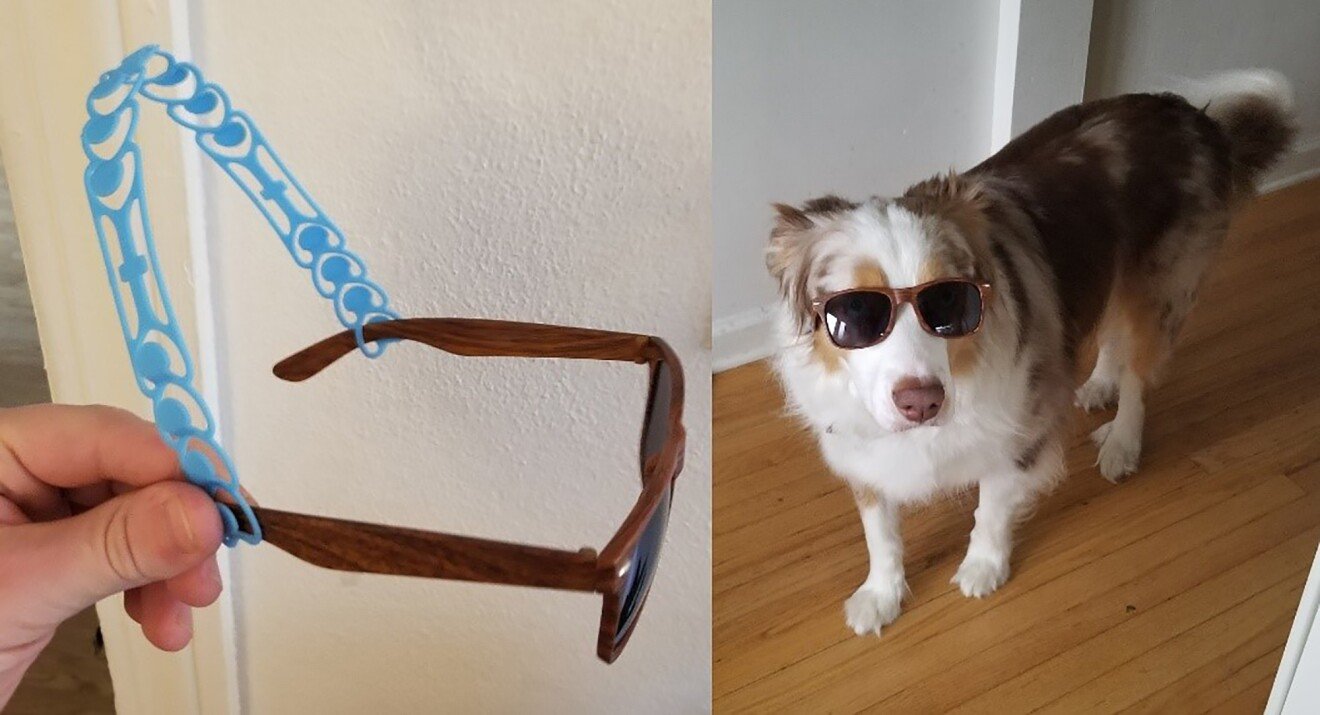